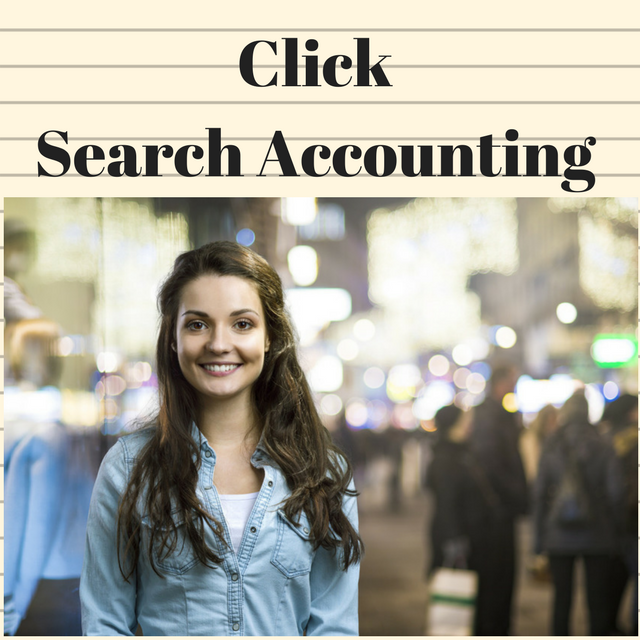
How to record full inventory cost for manufacturing company
There are three types of inventory for manufacturing company: raw material, work-in-progress (also known as work-in-process or abbreviation as WIP), and finished goods. Inventory is current asset.
Raw material inventory has not yet been put into production. They are stored in warehouse before covert them to work-in-progress (WIP) and finished goods. Raw material has two kinds: direct material and indirect material.It charged indirect materials to overhead, not to each job, because the company does not keep track of how much indirect materials it uses on each job.
Work-in-process (WIP) is inventory in the production process not completed 100 percent as finished goods at the balance sheet date.
Finished goods inventory includes all inventory units completed 100% as finished goods prior to the balance sheet date, and they are ready and available for sale.
For example, assume ABC manufactured table.
- Wood is material
- Table has three feet as work-in- process (WIP) because it is not completed as table.
- Table is finished goods because it is completed 100 percent.
Accounting for Inventory Cost
Accounting for Inventory Cost considers three main cost components. The first component is raw material, the second component is labor cost, and the third component is overhead.
Example
Assume that ABC manufactured Product A.
First step:
Company purchased material of $10,000. Accounting journal entry is as follows.
Dr. | Raw Material | 10,000 |
Cr. | Cash/AP | 10,000 |
Second step:
We assume that $2,000 of raw material is put into production; the following accounting entry to record raw material is made:
Dr. | Work-in-process | 2,000 |
Cr. | Raw material | 2,000 |
This journal entry is converted from raw material into the production process before raw material is stored at warehouse, so the raw material now become work-in-process( work-in-progress). This entry is for direct material while indirect material is absorbed to overhead.
Third step:
To convert the raw material into the production process, Company will need labor, so labor expense is incurred. We assume that $1,000 of direct labor incurred in the production process.
The following accounting entry to record direct labor of $1,000 is made:
Dr. | Work-in-process | 1,000 |
Cr. | Payroll | 1,000 |
To record the direct labor incurred to put material into production.
Fourth Step:
Finally, inventory cost must include factory overhead. Factory overheads include indirect material, indirect labor, and other overhead.
Factory overhead can be absorbed based on direct labor hour, machine hour, produced units, or %($) of direct cost.
For our case, we assume that for every $1 of labor cost, there may be $4 of overhead cost. Therefore, for every dollar of direct labor recorded in inventory cost, there will be $4 of overhead included in the cost of product or it means that factory overhead is 25% ( ¼) of direct labor cost.
The following accounting entry to record overhead of $4,000 ( $1,000 x 4) is made:
Dr. | Work-in-process | 4,000 |
Cr. | Factory overhead absorbed | 4,000 |
Fifth step:
Assume that Product A is completion and no beginning work-in-process (WIP). So we will transfer work-in-process to finished goods.
Work- in-process (WIP)= 2,000 + 1,000 + 4,000 = $7,000
Dr. | Finished Goods | 7,000 |
Cr. | Work-in-process | 7,000 |
Sixth step:
Assume that all Product A are sold of $10,000. Cost of finished good is $7,000 (Fifth step).
We can use period or perpetual inventory system for recording sale when inventories are sold.
Period Inventory System
Dr. | AR/Cash | 10,000 |
Cr. | Sale | 10,000 |
Under this system, cost of product sold will recognized at end of period.
Perpetual Inventory System
Dr. | AR/Cash | 10,000 |
Dr. | Cost of product sold | 7,000 |
Cr. | Sale | 10,000 |
Cr. | Finished Goods | 7,000 |
Under this system, cost of product sold will recognized at sale time.